WHAT WE DO
We provide the service of hot dip galvanization to iron, steel and ferrous alloys, to provide them with resistance to abrasion, environmental impacts and wear. Hot dip galvanization is a corrosion protection process that involves coating steel by immersing it in a bath of molten Zinc at a high operating temperature of a maximum of 650°C. This coating of a layer of tough, metallic Zinc on the steel surface covers and seals it from further oxidation and corrosive actions. Galvanization ensures a high coating strength of around 3600 psi and a double corrosion protection that is inclusive of sacrificial cathodic protection and barrier protection.
HOW WE DO IT
There are 3 fundamental steps in the hot dip galvanization process.
1. Surface preparation The surface of the steel is treated in order to increase its adhesion to coating.
2. Hot dip galvanizing
• Caustic solution or NaOH is a versatile alkali and acts as a degreaser. Steel is dipped in caustic solution, for about 5 to 8 minutes, to get rid of oil, grease, dirt and paint. The degreased steel is rinsed in water to remove excess caustic solution. • The rinsed degreased steel is dipped in Pickling solution (Pickle liquor), an acidic solution, for about 3 minutes (depending on the part requirement), to remove mill scale. Pickling is used to remove impurities, scales and inorganic components. Mill scale is the flaky surface of hot rolled steel, consisting of mixed iron oxides. The pickling solution is rinsed off.
• Wet scrubber is provided for extracting fumes from steel prepared.
• A flux is a low melting temperature organic chemical that is applied to steel to inhibit the oxidation of the cleaned surface upon exposure to air. The prepared steel is dipped in a hot or cold flux solution, like Zinc Ammonium Chloride solution, to protect from oxidation and dried on hot plate. The flux is allowed to dry on the steel and aids in the process of the liquid zinc wetting and adhering to the steel. Electrical energy is used for heating the hot plate & zinc melting furnace. Fume extractor hood near the zinc kettle is provided & connected to a common wet scrubber. The scrubber chimney height will be 3 meters above roof level.
• Prepared steel is dipped into the molten zinc bath and held there until the temperature of the steel equilibrates with that of the bath. The duration of dipping depends on the reaction time between Steel and Zinc. When reaction or bubbling stops, steel is lifted and moved to centrifuge, where excess zinc is removed by centrifugal force.
• The steel is cooled in a quench tank or dipped in a de-oxidant solution to reduce its temperature and inhibit undesirable reactions of the newly formed coating with the atmosphere.
3. Inspection The galvanized steel is inspected for galvanizing defects, in terms of the thickness of the coating, the adherence of the coating, the uniformity of the coating and its appearance.
1. Surface preparation The surface of the steel is treated in order to increase its adhesion to coating.
2. Hot dip galvanizing
• Caustic solution or NaOH is a versatile alkali and acts as a degreaser. Steel is dipped in caustic solution, for about 5 to 8 minutes, to get rid of oil, grease, dirt and paint. The degreased steel is rinsed in water to remove excess caustic solution. • The rinsed degreased steel is dipped in Pickling solution (Pickle liquor), an acidic solution, for about 3 minutes (depending on the part requirement), to remove mill scale. Pickling is used to remove impurities, scales and inorganic components. Mill scale is the flaky surface of hot rolled steel, consisting of mixed iron oxides. The pickling solution is rinsed off.
• Wet scrubber is provided for extracting fumes from steel prepared.
• A flux is a low melting temperature organic chemical that is applied to steel to inhibit the oxidation of the cleaned surface upon exposure to air. The prepared steel is dipped in a hot or cold flux solution, like Zinc Ammonium Chloride solution, to protect from oxidation and dried on hot plate. The flux is allowed to dry on the steel and aids in the process of the liquid zinc wetting and adhering to the steel. Electrical energy is used for heating the hot plate & zinc melting furnace. Fume extractor hood near the zinc kettle is provided & connected to a common wet scrubber. The scrubber chimney height will be 3 meters above roof level.
• Prepared steel is dipped into the molten zinc bath and held there until the temperature of the steel equilibrates with that of the bath. The duration of dipping depends on the reaction time between Steel and Zinc. When reaction or bubbling stops, steel is lifted and moved to centrifuge, where excess zinc is removed by centrifugal force.
• The steel is cooled in a quench tank or dipped in a de-oxidant solution to reduce its temperature and inhibit undesirable reactions of the newly formed coating with the atmosphere.
3. Inspection The galvanized steel is inspected for galvanizing defects, in terms of the thickness of the coating, the adherence of the coating, the uniformity of the coating and its appearance.
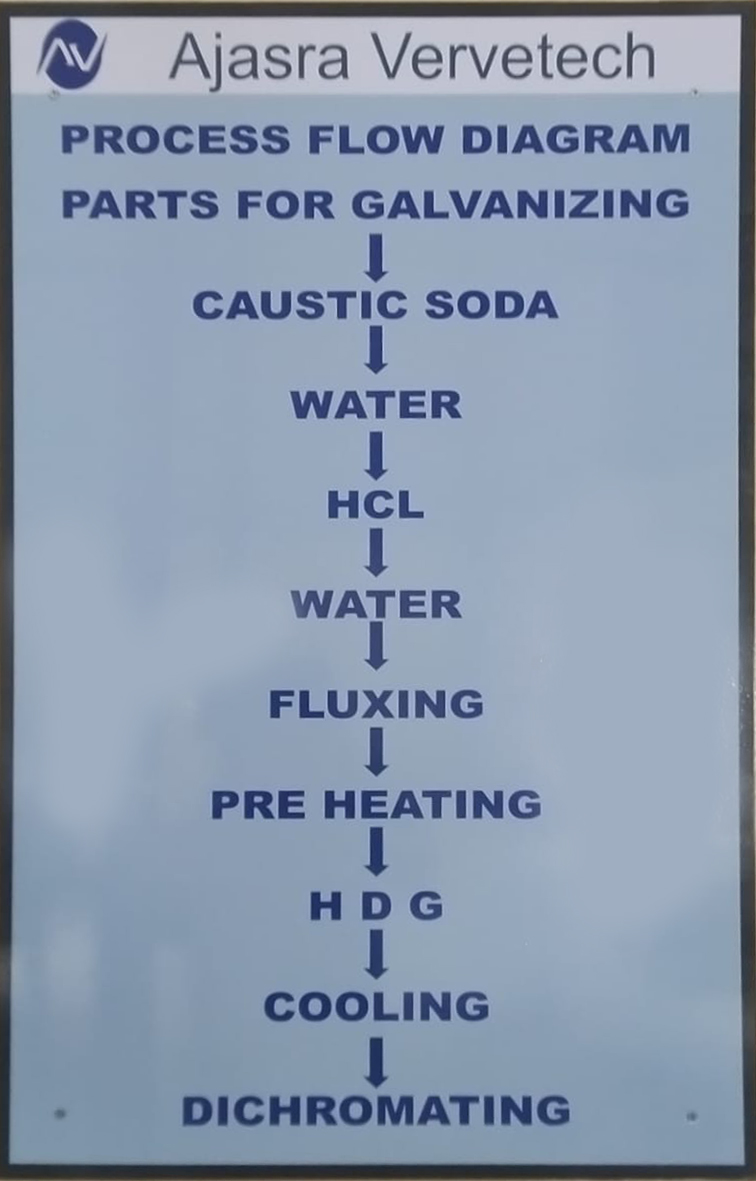